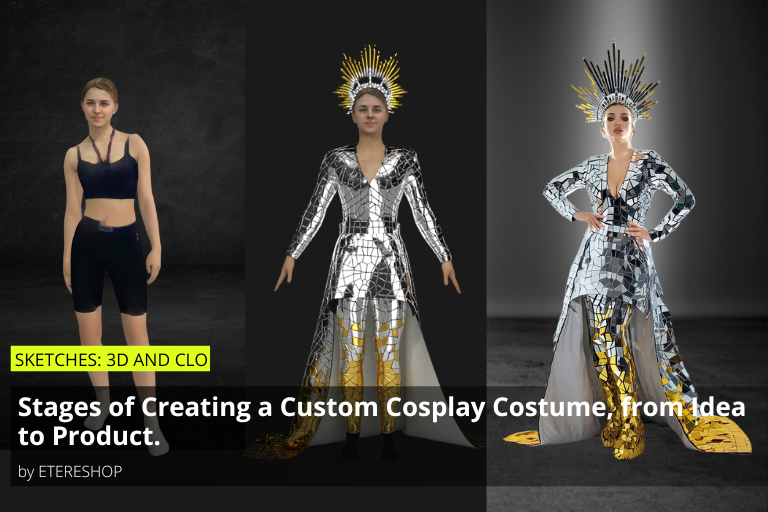
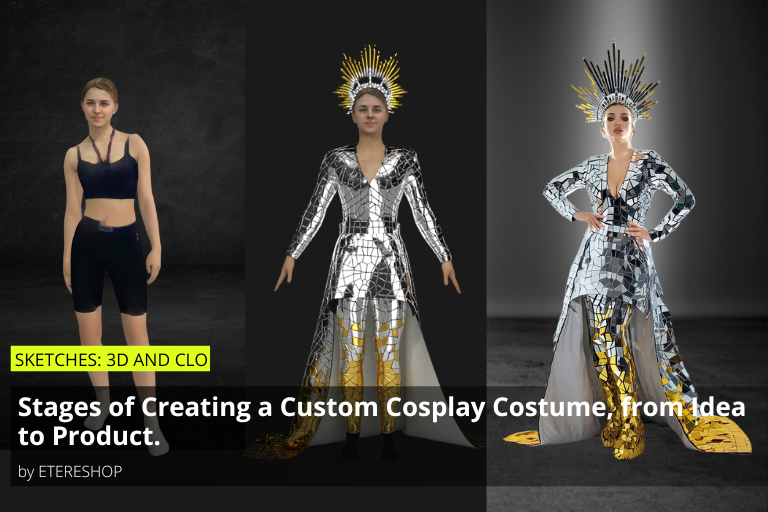
Home » Blog » 2022 » Stages of Creating a Custom Cosplay Costume, from Idea to Product – by ETERESHOP
Creating a custom cosplay costume is not a simple task, but interesting and challenging. With an experienced team and smart apps there is no need to go to a fitting – the suit will suit like a glove and look perfect. Do you want to know how we do it and what are the stages of creating a suit in our company?
If you doubted that you could order a custom outfit and get it without trying on, but perfectly suited to your figure, just read this article and you will understand why the exclusive custom-made cosplay suit will fit you completely.
So, you’ve decided to order a custom cosplay outfit, but don’t know where to start. The first thing our company starts with is asking you to make your own avatar. This is done so that your custom order suit fits perfectly on your figure. The avatar is the parameters of your body that are necessary for the perfect size of the custom cosplay suit.
We strictly recomment to collect the hair at the top of the head. Otherwise the program scans it with the body into one large object and there will be a hump on the neck and back. We also request to use the tightest leggins for scanning clothes to correctly convey the outlines of the body, and it is good for scanning to do this in a well-lit room, then you will get the maximum quality.
Each detail of the exclusive custom-made costume is modeled separately. Now the main thing is creative design and show the client how his new image will look like. The main instrument of our custom suit designers is the CINEMA 4D PROGRAMM application and the CLO3D application. The first is for rigid forms, the other is for clothes where patterns are needed.
Custom Cosplay 3D outfit is created in CLO3D programm. We take a ready avatar and adjust the parameters of the body to the parameters of the customer. Program allows us to create perfectly tailored clothes, try them on and check the fit in motion. So we end up with a very cool result and show a perfect fitted suit for each specific client.
Then we send renderings to the client – sketches transferred from 3d space to a regular image, or we make a screen recording and spin around when there is a need to show some details in dynamics. The client does not need skills, the program for scanning the body is enough with a simple instruction.
You can immediately see yourself in the requested custom cosplay costume and make changes to the design even at the sketch stage, 3D helps to show the product more realistically on the body than just a drawn sketch, since it is made on a thin body and special lengthens the legs, and customers’ bodies are different.
Cons of body scanning – it does not exactly allow to take a body scan as a basis for a suit, customer measurements nevertheless are required, since there are errors in dimension during scanning. The program changes hands on its own – scanning fingers into a fist, at the output a model with an open palm.
Patterns are unloaded from this program and transferred to production along with images.
In this department in the AUTOCAD program, they prepare the cutting of the product. Mirror acrylic or any other fabric or material is cut out for further joining into a finished costume element.
The eve foam or mirrored acryl, from which the product is made will be cut by a laser.
The program not only helps to create a costume, break it down into details and colors, but also suggests the exact amount of material for its accurate calculation. In addition, the program offers different color solutions.
The CLO3D program allows not only to break the costume into parts, calculate the material and show different color schemes, but also allows the avatar to move in the costume to show it in all glory. This is a great opportunity to see how the suit will fit you.
More information about creating 3d custom costumes can be found in the article “3D modeling of costumes for preliminary demonstration of the product”.
We send the final version to the customer for approval. After that we send the patterns for production. This process includes ordering and purchasing materials, cutting and making a costume. It all depends on the complexity of the work and the search for material.
After the sketch was approved by the customer, we began to develop a pattern in CLO and apply the product to the fabric.
According to the patterns, we make drawings of the cut of the mirrors, determine the dimensions of the mirrors and their location. We create a suit from the selected fabric.
The patterns are transferred onto the canvas in the sewing shop, where the pieces of fabric are carefully sewn together to become a costume.
Biflex stitched according to patterns. Based on the printed patterns, a base is sewn on which mirrors will subsequently be glued.
The ready sewn costume still needs to be decorated with mirrors. After that the pieces of silver mirror and gold and green acrylic glass are manually glued onto the fabric, strictly following the predesigned pattern.
Upon completion of the manufacture of the product we need to make sure that absolutely all the client’s requirements have been taken into account. Fitting a ready-made suit for approval with the client.
The whole process, from the first call to the delivery of the product to your address, is carried out by one employee. You will always be aware of the stage of creation of your custom cosplay costume. In addition, if there is an urgency, we will try to fulfill your order strictly on time. If you still have questions about how we make custom costumes, then feel free to write them. And if there are no questions left, then contact us and order your new outfit by sending your ideas.
We hope that the article about creating custom orders in ETEREshop was useful for you and we will be pleased if you share it with your friends.